ENDUREIT. Efficient design of steel with excellent durability at intermediate temperature
Background
Duplex stainless steels have an attractive combination of high strength and corrosion resistance, making them a suitable choice in applications such as pressurized equipment in the nuclear, chemical and pulp & paper industry. Increased efficiency in these applications is linked to higher service temperatures, but the current service temperature of duplex stainless steels is limited to about 250 °C. The reason is that the material is embrittled above this temperature due to phase separation, where the alloying elements Fe and Cr demix. Phase separation has been studied for a long time in ferritic alloys, but less work has been performed on commercial duplex alloys, especially on how to mitigate the embrittlement. The reason for the scarcity of previous works is because of the difficulty to study the underlying phenomenon using existing tools. However, in the last decade developments in experimental and computational tools have been significant. KTH has contributed to this development over the last decade via the Excellence center Herom, which has been working on the development of tools for integrated computational materials design. Outokumpu AB has been one of the industrial partners within Herom and both KTH and Outokumpu AB have been very active in the field of intermediatetemperature embrittlement of stainless steels within the Herom center. Firstly, simple model alloys of FeCr with the same underlying phenomenon were investigated and more recently duplex stainless steels have been the focus. In that work significant progress has been made when it comes to both development of materials design tools as well as the understanding of the intermediatetemperature embrittlement of duplex alloys. Therefore, in 2017 a Booster project funded by EIT Raw Materials was launched by KTH and the spinoff company Ferritico AB in collaboration with Outokumpu AB to investigate whether the knowledge could be applied for the design of a new duplex alloy that is less sensitive to intermediatetemperature embrittlement. Within that project we have been able to develop a new duplex stainless steel alloy that has an estimated prolonged lifetime of about two times compared to conventional duplex stainless steels. The alloy has been produced in pilot scale by Outokumpu Stainless Oy. The estimated performance of the alloy is unprecedented and would provide a major competitive advantage for stainless steel producers as well as endusers in e.g. chemical and nuclear industries. Furthermore, the alloy design methodology that has been applied within the project has enabled an extremely short development time of about nine months. This would not be possible using conventional alloy design, and if the efficiency of the design methodology can be validated by bringing the solution all the way to implementation, it would be a major advancement for the development of stainless steels in general. To fully validate the new alloy design methodology and the new alloy solution, it is necessary to upscale the solutions.
The partners of the project are KTH, Outokumpu Stainless, Outokumpu Oyj, CEA and Ferritico.
Purpose and aim
The overall aim of this proposal is twofold: i) to upscale a novel duplex stainless steel alloy solution that is less sensitive to intermediatetemperature embrittlement, enabling the usage of the high performance duplex stainless steel alloy category above service temperatures of 250 °C, and ii) to upscale the alloy design methodology, combining computational tools, large databases and miniaturized experiments, to enable significantly more rapid development of stainless steels in general, and duplex stainless steels in particular.
Project plan
The project is divided in 6 work packages shown in the Gantt chart.
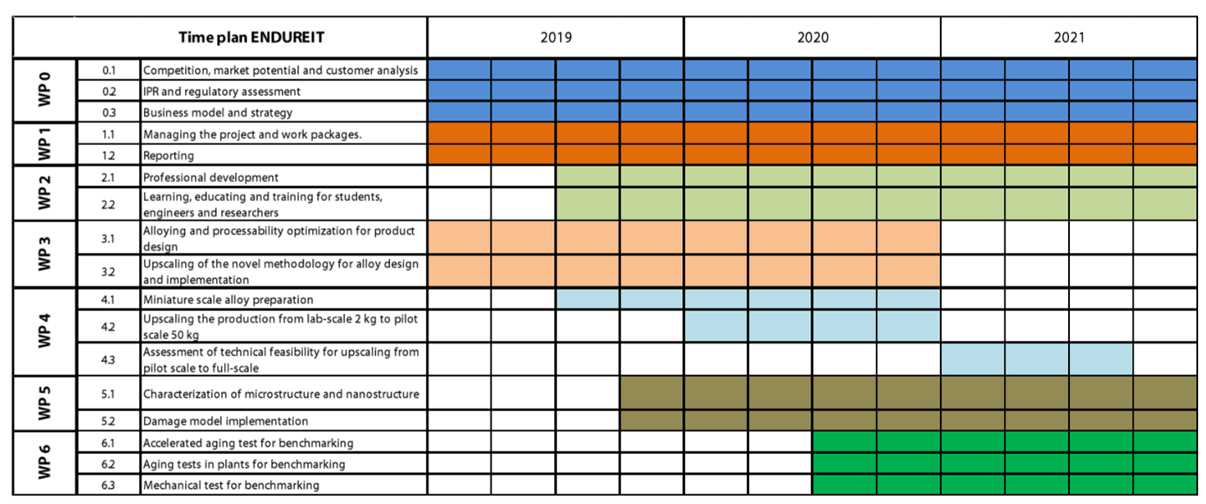
Funding agency
EIT Raw Materials Upscaling.
Beginning and end dates
2019-01-01 to 2021-12-31
Project contacts
More information
N/A