"We can produce steel with one-tenth of the electricity"
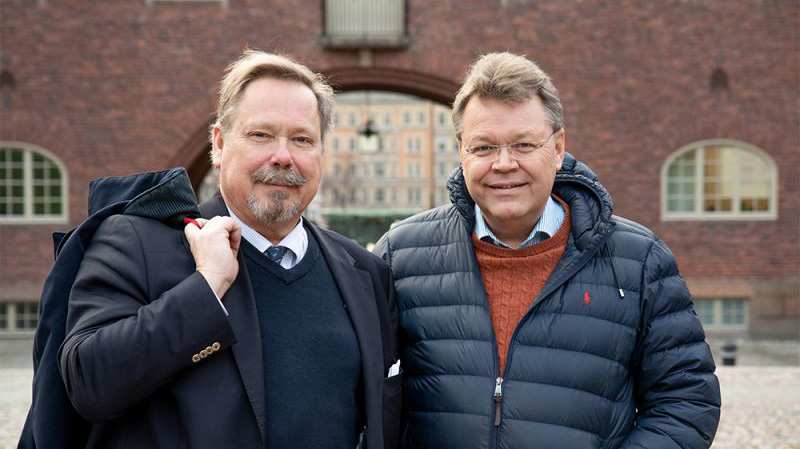
FerroSilva, which started as a project at the Department of Materials Science and Engineering, has developed a new process for producing fossil-free sponge iron. The plan is to start the first factory at Ovako's facility in Hofors asap, with the planned start of operations in 2026
"We can produce steel with one-tenth of the electricity required." That's stated by Peter Samuelsson , Rutger Gyllenram, and Göran Nyström in a debate article in Dagens Industri.
FerroSilva, which started as a project at the Department of Materials Science and Engineering at KTH, has developed a new process for producing fossil-free sponge iron. The input product is residual products from forestry and agriculture. Out of the forestry industry's rejected tree tops and branches (“grot”) - roughly twenty million tons each year - a small part will be converted into the gas that is the primary energy source in the manufacturing process.
"Producing fossil-free sponge iron based on hydrogen is a very electricity-intensive method. The FerroSilva process requires less than a tenth of the electricity per produced ton of sponge iron compared to the electrolysis-based initiatives since most of the input energy is stored in the forest residues that gasify," says Peter Samuelsson.
“Globally, one tonne of finished steel has generated an average of two tonnes of carbon dioxide emissions; with our process, three tons of carbon dioxide would be saved for every ton of finished steel.”
The process is particularly suitable for countries with good access to biomass and where access to electricity is a limiting factor.
"The plan is to start FerroSilva's first factory at Ovako Group's facility in Hofors as soon as possible, with the planned start of operations in 2026."
Read the full text in Dagens Industri: Debatt: Vi kan tillverka fossilfritt stål med en tiondel av elbehovet