High energy X-rays reveal the resistance of steel to embrittlement
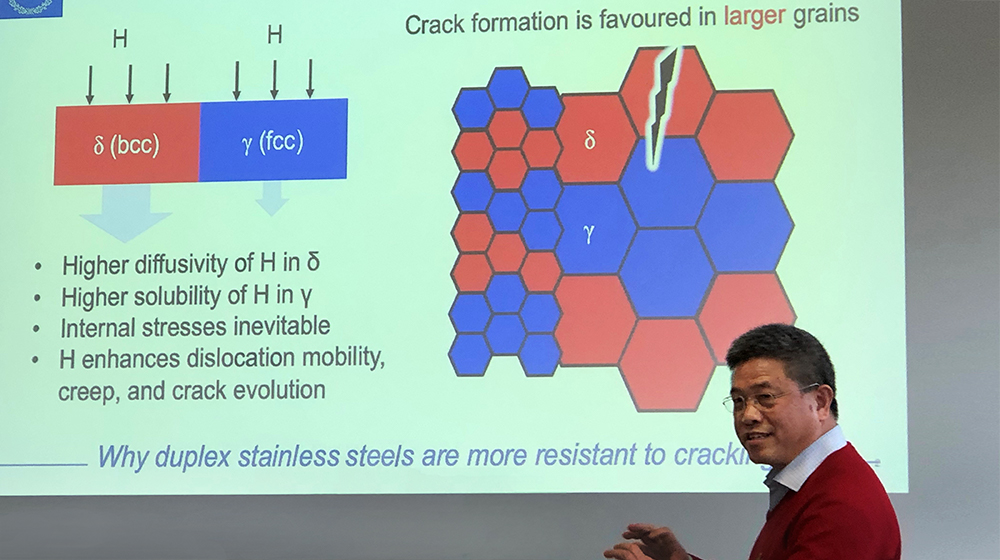
Impact stories
The high energy X-rays at the Swedish Material Science beamline make it possible to see what’s happening within steels, in real-time, also in environments that mimic how the steel is used. This enabled researchers from KTH and Sandvik Materials Technology to find out why steels from Sandvik are more resistant to hydrogen embrittlement than other steels.
Swedish steel companies use know-how to develop and offer specialist steels for safe and lasting use in challenging environments.
The challenge in offshore environments is exposure to hydrogen, which makes steels brittle – a problem identified as long ago as 1875.
Researchers have since worked to develop steels that are more resistant to hydrogen embrittlement. Such resistance to embrittlement was therefore a key aspect of one special steel that Sandvik developed and now sells worldwide – with users recognising that this Sandvik steel is longer-lasting than competitors’ steels when used offshore.
However, researchers couldn’t fully explain why Sandvik steels perform better – it just wasn’t possible to understand the details of hydrogen-microstructure interaction that leads to embrittlement with laboratory research techniques.
The explanation emerged in one of the first uses of the Swedish Material Science beamline in 2019. At the Swedish Material Science beamline, high energy X-rays can penetrate steels, enabling researchers to map the hydrogen-induced changes in structure within the steels – and how those structural changes vary with time – in environments that mimic how the steel is used.
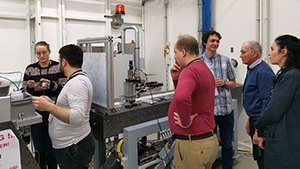
Researchers from KTH and Sandvik Materials Technology, therefore, exposed the steel samples to hydrogen and placed these steels under stress – and studied how hydrogen rapidly moves within and interacts with the steel, as well as how the steel’s internal structure evolves.
Duplex stainless steel and other duplex steels from Sandvik comprise two phases: the body-centered-cubic (bcc) phase and the face-centered-cubic (fcc) phase. There are very many grains of these fcc and bcc phases distributed in a complex pattern within the steels. The synchrotron measurement results show that hydrogen can quickly enter the duplex stainless steel – but cause different changes in the two phases.
The results also provided new knowledge: hydrogen causes more deformation of the fcc phase, which can dissolve more hydrogen than the bcc phase, although hydrogen diffuses much faster through the bcc phase.
The fact that these phases interact so differently with hydrogen is important: the boundary regions between the fcc and bcc phases accommodate more hydrogen and withstand more internal stress. The coordinated response of the two phases, like load sharing, hinders the initiation of micro-cracks, thus providing high resistance against embrittlement.
The experiments at the Swedish Material Science beamline were the first time that these hydrogen-microstructure interactions were observed in real-time.
The experimental results also showed that the duplex stainless steel with finer microstructure is less sensitive to hydrogen embrittlement. The fine microstructure size is important: the phase boundary area within the steel, and hence the beneficial effect of hindering crack initiation, increases significantly with decreasing phase area size.
Accordingly, with their finer microstructure, Sandvik seamless tubes are significantly more resistant to embrittlement than steels with a coarser microstructure.
Sandvik can use this information in technical sales, as well as future R&D. Researchers are now able to explain the phenomenon of hydrogen embrittlement of duplex stainless steels scientifically. This case illustrates how advancing scientific knowledge, solving old problems and supporting industry, can go hand in hand.
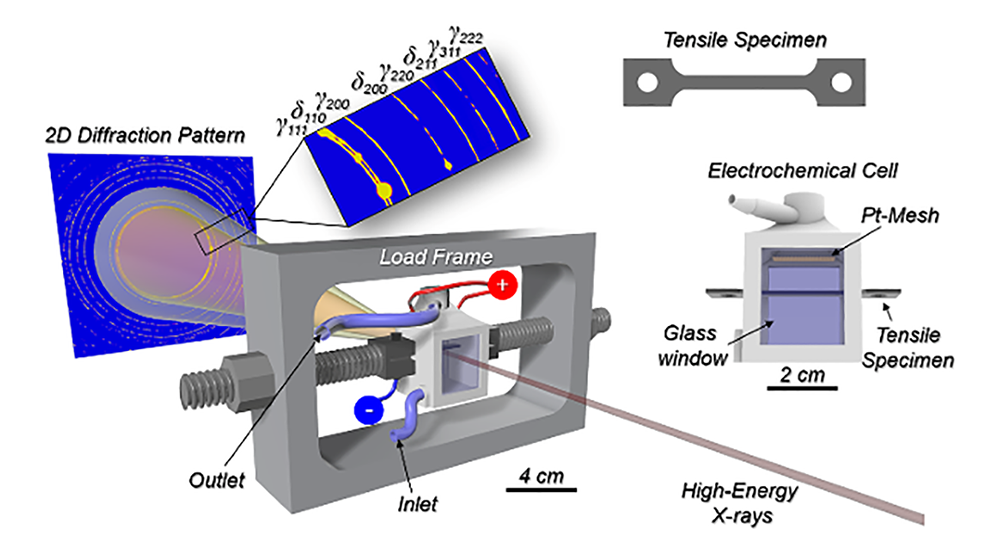